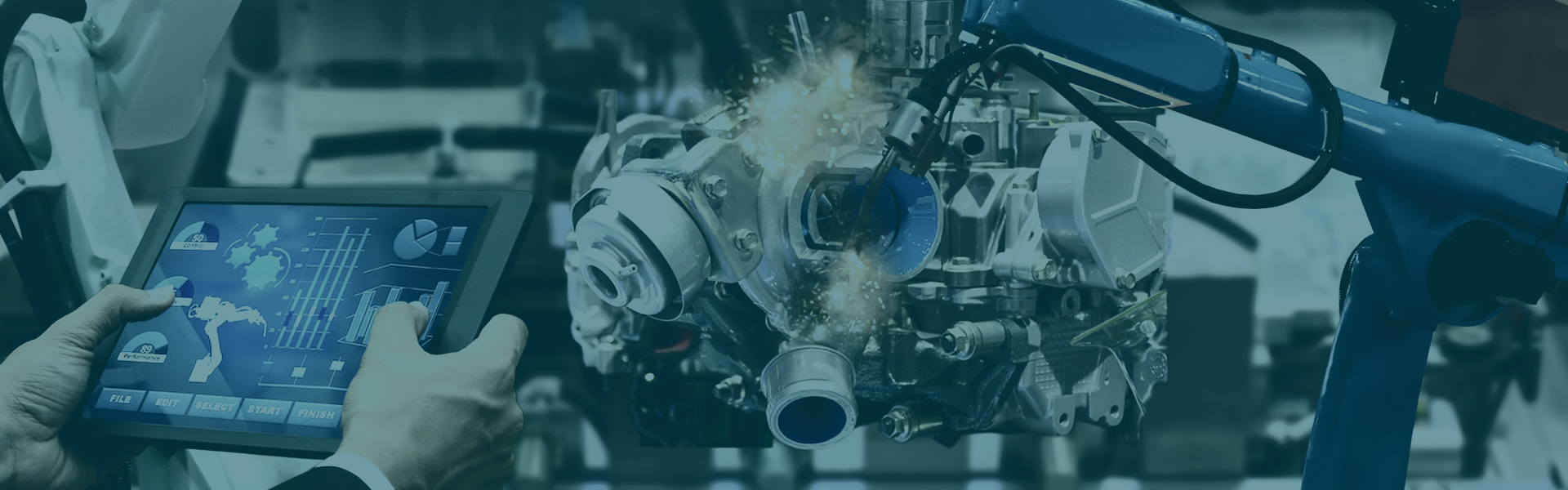
INDUSTRIAL Y ROBÓTICA
El Grupo de Automatización Industrial y Robótica, integrado en el Instituto de Diseño y Fabricación y en la Asociación IDF de Inteligencia Artificial y Robótica, es un grupo de investigación formado por profesores e investigadores del Departamento de Ingeniería de Sistemas y Automática de la Universidad Politécnica de Valencia.
Dentro de este grupo, se contempla la investigación en aspectos tan dispares como: sistemas de toma de toma de datos y monitorización; la automatización de procesos industriales; la simulación de sistemas; el diseño de estrategias de control, incluyendo el control supervisor; el modelado, análisis y simulación de sistemas, además de la identificación de parámetros, la estimación de variables, las técnicas de análisis basadas en tiempo y en frecuencia y los lenguajes específicos de simulación.
Durante años, el Grupo AIR ha realizado investigación, al tiempo que colaborado con empresas en temas tales como el diseño y fabricación de máquinas especiales (ensamblaje de piezas, inserción de muelles, máquina de machihembrado, máquina de pegado de madera, etc.). también ha trabajado en el diseño y fabricación de herramientas y utillajes. Además, utiliza sensores para una amplia gama de aplicaciones, que van desde el caso del cálculo volumétrico de la carga en camiones al estado físico de conductores en autobuses.
En paralelo con los trabajos anteriores, el Grupo AIR se ha destacado en dos grandes líneas de investigación:
-
- Robótica Industrial, Robótica Móvil y Robótica Colaborativa, además de Sistemas de Conducción Automatizada.
- Automatización de Procesos y Control de Calidad basados en Técnicas de Fusión Sensorias, Visión por Computador e Inteligencia Artificial.
En lo referente a Robótica Industrial, se apoyan proyectos de investigación relacionados con la fabricación mediante robots, integrando CAD-CAM-Robótica, todo ello cara a la fabricación automatizada de productos de gran volumen. Para potenciar esta actividad se cuenta con dos importantes laboratorios: LABORATORIO DE ROBOTICA FLEXIBLE y el LABORATORIO DE IMPRESION 3D-MACRO. Resaltar que el track lineal de Laboratorio de Robótica mide 7,2 metros y el Laboratorio de Impresión capaz de realizar piezas y moldes de tamaño MACRO (2.500cm x 1.500cm x 1.000cm).
En lo referente a Robótica Móvil se incluyen trabajos de automatización de carretillas elevadoras para la automatización de almacenes, así como apoyo al desarrollo de sistemas de conducción autónoma. Esta línea de investigación que dio muy buenos resultados en el pasado está desactivada pendiente de nuevos retos concretos.
No obstante, hay que destacar que en dicha línea se desarrollaron interesantes soluciones de cinemática y dinámica de vehículos, como aparcamiento automático, detección y seguimiento de objetos y autolocalización de robots móviles, detección y evitación de colisiones, construcción de mapas del entorno, planificación de movimientos y de tareas, etc.
Vale la pena citar el ORCA300, vehículo submarino de 3 metros de eslora equipado con cuatro motores, equipado con dos cámaras para tareas de inspección y visual servoing, así como de una IMU para el posicionado del vehículo y un sonar para reconstrucción del entorno. También se ha usado en tareas de inspección, posicionamiento, atraque, seguimiento de tuberías para reparación, etc.
Actualmente y en el contexto de Robótica Colaborativa, se esta investigando sobre los procesos de realimentación de fuerza para el pulido industrial de superficies mediante un sistema de robot con suficiente inteligencia para ayudar al operador humano a realizar correctamente la tarea y mejorar la calidad, productividad y ergonomía del proceso.
Para el desarrollo de la investigación, se dispone de tres plataformas robóticas con las que realizar la experimentación.
La primera plataforma está basada en un robot colaborativo “Kuka LBR iiwa”, dotado de un sensor de fuerza “IIT FT-45” acoplado a un modelo de herramienta de pulido, una cámara de visión 3D “Intel RealSense D435” y una PC industrial “omron NYP27”; en ella se prueban algoritmos de control no convencionales de fuerza que eviten por un lado el desgaste de la herramienta y la superficie debido a la operación de contacto, y por otro que eviten el desgaste o rotura de la herramienta durante su deslizamiento por la superficie.
La segunda plataforma está basada en un robot industrial “Kuka KR6”, montado sobre una plataforma móvil de un grado de libertad que se desplaza a lo largo de la parte superior de una estructura metálica que actúa como celda de contención, tres cámaras “Kinect” de visión 3D y un sensor de fuerza “ATI Axia80” acoplado a un modelo de herramienta de pulido; en ella se prueban tanto leyes de control de fuerza no convencionales y planificación de trayectorias aplicadas a robots en el tratamiento de anomalías superficiales, como técnicas de visión 3D para la detección de obstáculos y posicionamiento de piezas en el área de trabajo.
La tercera plataforma robótica es la constituida por el robot industrial “Kuka KR10” con un sensor de fuerza “OptoForce Hex E” acoplado y una PC “msi Infinite s” que forman parte de un prototipo de túnel de inspección mediante visión artificial para la detección de defectos; en esta plataforma se prueba, a parte de las leyes de control no convencionales y la planificación de trayectorias, la comunicación e intercambio de información entre los sistemas de detección y clasificación de defectos mediante visión artificial con el robot.
En el contexto de la Automatización Industrial y Control de Calidad, se trabaja con sistemas de telemedida, teleoperación y telecontrol, con integración de sensores tales como scanner láser, cámaras de visión artificial e infrarrojos, sensores de ultrasonidos, etc. Todo ello sin descuidar los aspectos de simulación 2D, 3D y realidad aumentada.
Estos sistemas se utilizan tanto en labores de supervisión del proceso productivo como en el control de calidad de los productos manufacturados.
En lo referente al control de calidad para la mejora de productos y procesos, se vienen desarrollando novedosos sistemas de inspección automatizada de superficies mediante técnicas de visión artificial con procesamiento paralelo y computación distribuida que detecta tanto microdefectos (de hasta 0.2 mm de diámetro) como macrodefectos casi imperceptibles.
El primer prototipo industrial, que se muestra a continuación, estuvo en fase de validación desde el 2008 en la Factoría FORD de Almussafes durante casi 2 años, llegando a inspeccionar hasta 1.700 coches/día, uno de los momentos de mayor producción de dicha Factoría.
Desde el punto de vista de implementación, los sistemas deberán incorporar sofisticados algoritmos de inteligencia artificial, tanto en el proceso de diseño óptimo del túnel como en el calibrado de cámaras y luces; autoajustes de iluminación y otras condiciones ambientales; además de otros algoritmos pare el reconocimiento, identificación y clasificación de defectos, entre otras tareas.
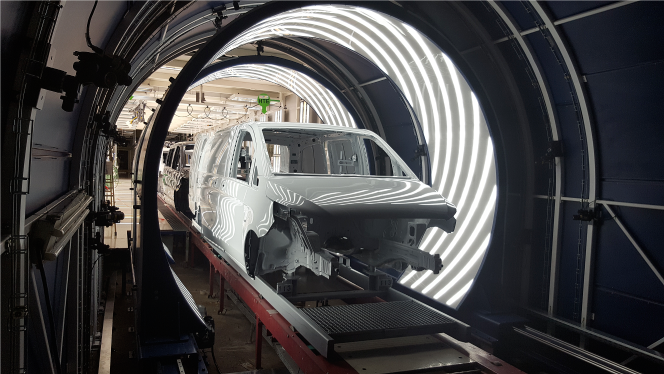
Indicar que el éxito obtenido en la transferencia de tecnología se ha debido a un buen maridaje entre el Grupo de Investigación y empresas de ingeniería implicadas. Y, así pues, las primeras implantaciones en Factorías FORD se realizaron a través de dos empresas valencianas (ICEMI, ingeniería electromecánica, y AUTIS, ingeniería de automatización, control y comunicaciones) y en la actualidad las dos nuevas implantaciones se realizan a través de otras dos empresas, también valencianas.
Estos nuevos sistemas de inspección, acuñados como Q-EYE, son capaces de detectar microdefectos tanto en áreas planas como en zonas complejas como bordes de piezas, zonas cóncavas como manetas y líneas de estilo, cada vez más frecuentes en los nuevos modelos de vehículos.
Los túneles están formados por dos estructuras: una externa fija albergando hasta 30 cámaras capaces de inspeccionar todos los rincones de la carrocería, y una interna móvil con pantallas LED de alta resolución y alta potencia, que producen un barrido sobre la carrocería resaltando todos los defectos existentes.
Como se muestra en la imagen, las pantallas LED son capaces de proyectar cualquier figura móvil constituyendo un perfecto sistema de iluminación virtual, en donde más de medio millón de LEDs son controlados independientemente en todo momento.
El sistema consta principalmente de: 1) un controlador (PLC) para el movimiento de la estructura móvil y para la identificación de la carrocería entrante, así como garantizar todas las seguridades exigidas; 2) un computador especializado en visión dotado con tarjetas de computación paralela son capaces de procesar los 300GB que se generan por cada carrocería inspeccionada; 3) un computador de gestión de la BBDD así como la comunicación con el sistema de información de planta, cara a poder procesar las aplicaciones estadísticas (Statistics), de BI (Business Intelligence) y BD (Big Data), en el contexto de la transformación digital de la Industria 4.0.
Y en ese contexto de Industria 4.0, se agradece en especial el apoyo y la confianza de los ingenieros y directivos de Mercedes-Benz Vitoria en la búsqueda de sistemas innovadores que pudieran constituir referentes dentro de la compañía a nivel mundial.
Y finalmente en lo que concierte al mecanizado mediante robots, se tiene una celda robotizada (2 robots) implantada en la factoría FORD de Almussafes para el lijado suave de los capós de todos los vehículos que se fabrican en dicha factoría utilizando algoritmos de inteligencia artificial desarrollados en el seno del Instituto de la UPV.